Hardfacing Cored Wires
BMI Cored Wires combine innovation and performance to meet the most demanding industrial requirements.
Designed to provide exceptional resistance to abrasion, wear, and impact, these wires ensure long-lasting protection for critical equipment.
Each product is specifically formulated for targeted applications, whether for extreme conditions or moderate wear.
FCW63®
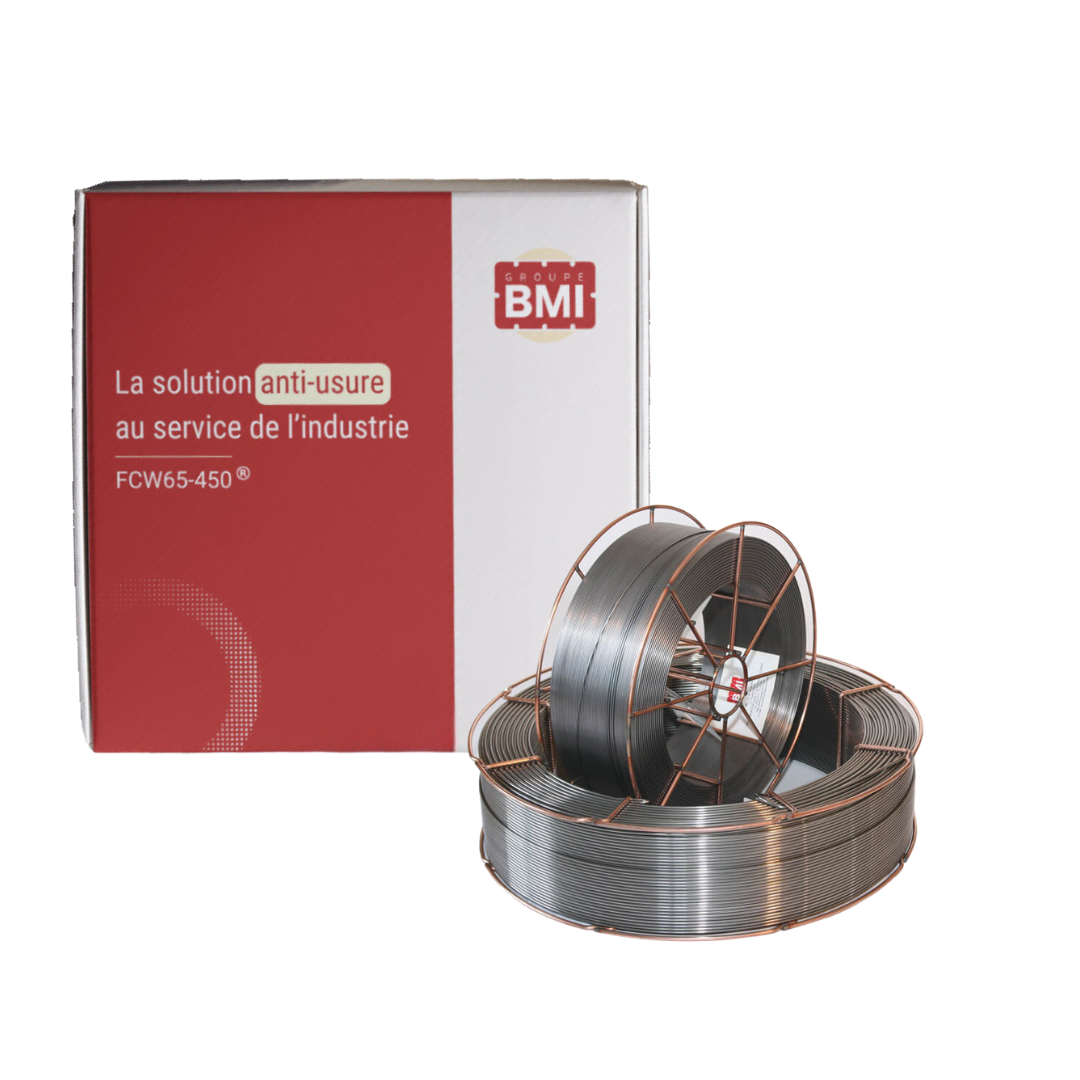
Characteristics
Welding Type: Hardfacing cored wire for open-arc welding (self-shielded, slag-free).
Composition:
- Carbon (C): 4.8%
- Manganese (Mn): 1.2%
- Silicon (Si): 0.6%
- Chromium (Cr): 29%
Hardness:
- 1st layer: ~58 HRC
- 2nd layer: 60-63 HRC
Available Diameters:
- Ø 1.6 mm, Ø 2.4 mm, Ø 2.8 mm
Advantages
Exceptional abrasion resistance due to a high chromium carbide content.
Up to 50 times more effective than conventional electrodes of equivalent hardness.
Smooth fusion, optimal spread, and very even bead appearance.
Slag-free deposit, machinable by grinding or polishing.
Suitable for parts exposed to low to moderate impacts.
Applications
- Overlay Plates
- Grinding and Mineral Conveying Components
- Dredging Pumps
- Mixers
- Screen Plates
FCW63B®
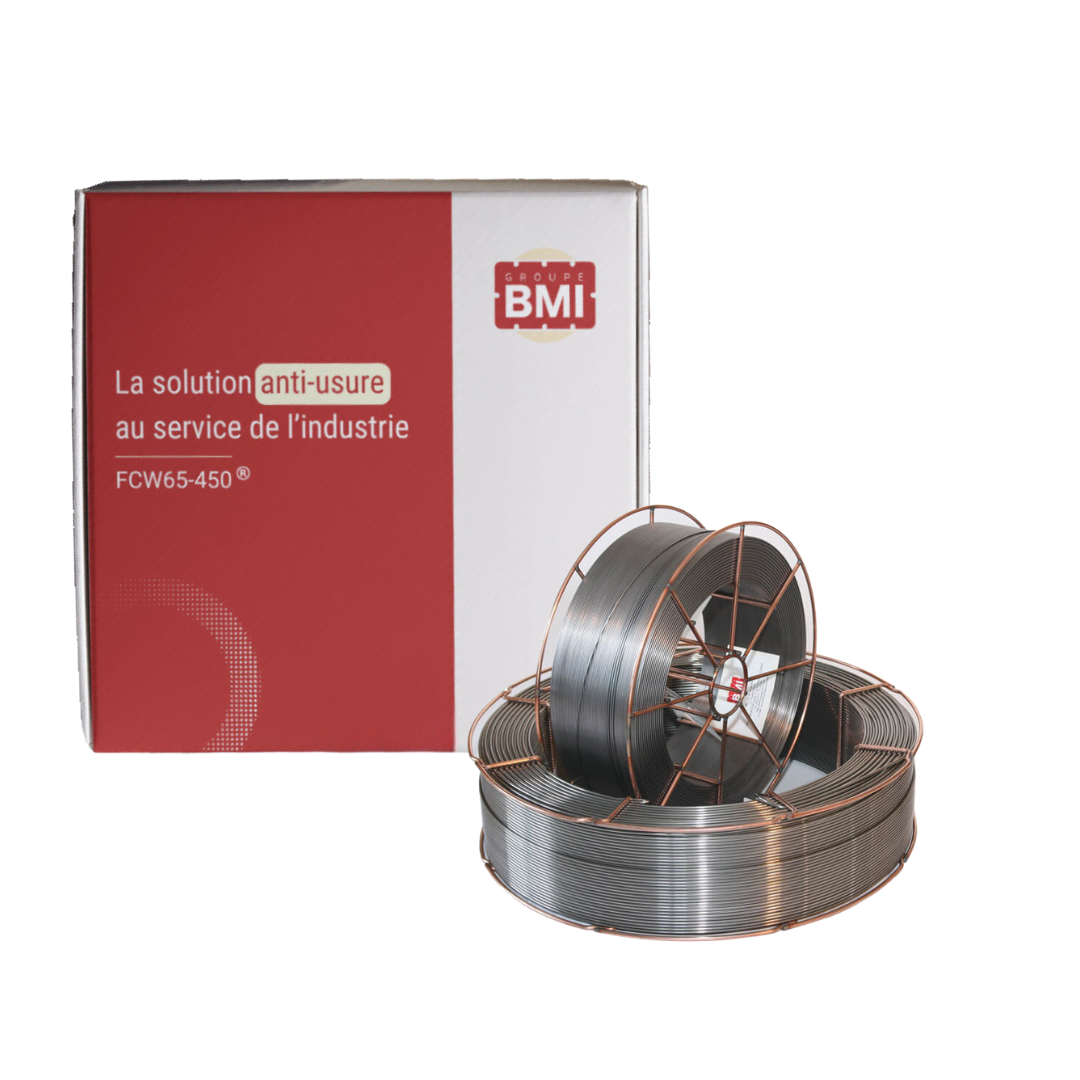
Characteristics
Welding Type: Hardfacing cored wire for open-arc welding (self-shielded, slag-free).
Composition:
- Carbon (C): 5.0%
- Manganese (Mn): 1.5%
- Silicon (Si): 1.5%
- Chromium (Cr): 27%
- Boron (B): 0.4%
Hardness:
- 1st layer: ~60 HRC
- 2nd / 3rd layer: 63-65 HRC
Available Diameters:
- Ø 1.2 mm, Ø 1.6 mm, Ø 2.4 mm, Ø 2.8 mm
Advantages
Excellent abrasion resistance due to a high chromium carbide content.
Up to 50 times more effective than conventional electrodes of equivalent hardness.
Smooth fusion, optimal spread, and very even bead appearance.
Slag-free deposit, machinable by grinding or polishing.
Suitable for parts exposed to low to moderate impacts.
Applications
- Overlay Plates
- Grinding and Mineral Conveying Components
- Dredging Pumps
- Mixers
- Screen Plates
FCW65-450®
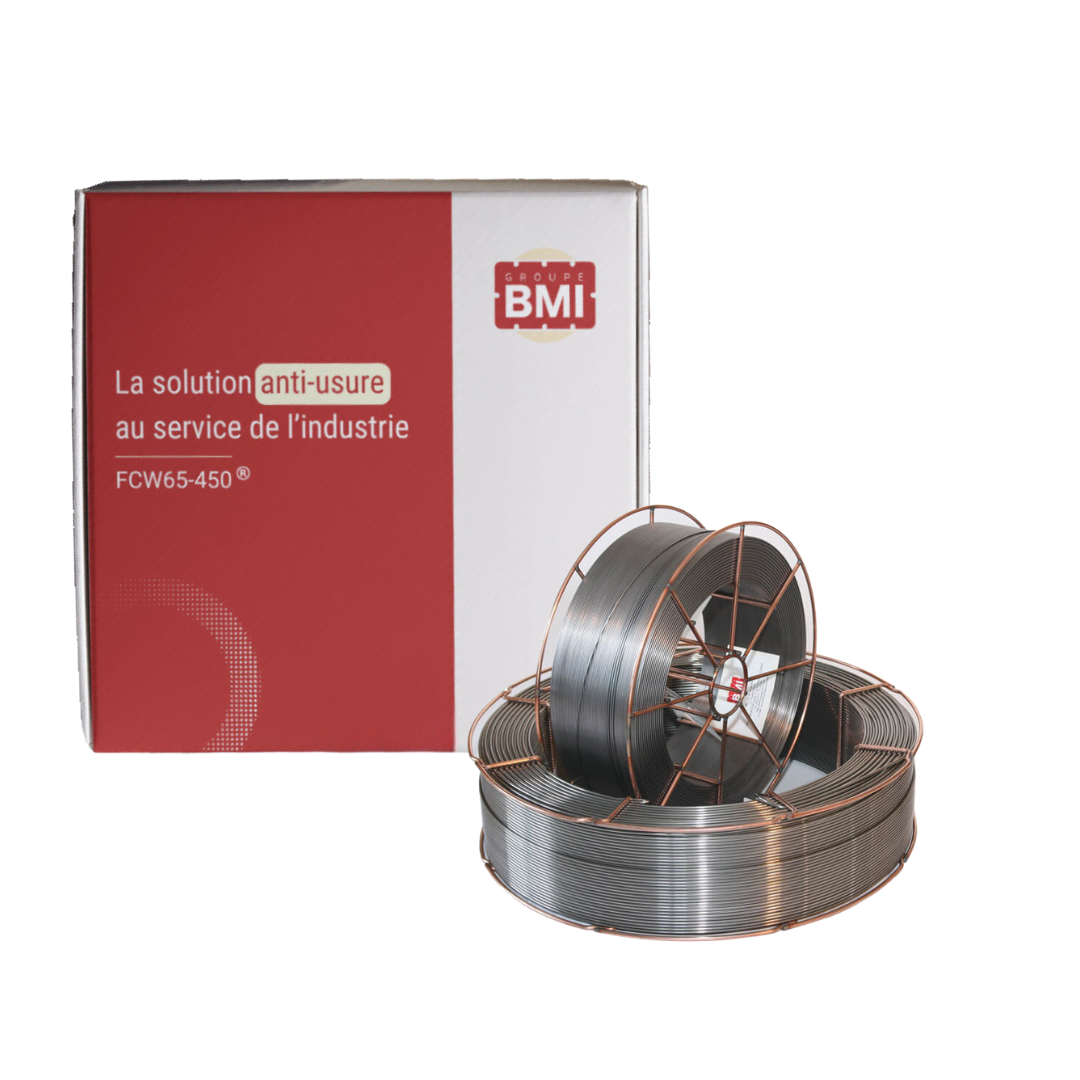
Characteristics
Welding Type: Open-arc (self-shielded, slag-free).
Composition:
- Carbon (C): 4.6%
- Manganese (Mn): 0.2%
- Silicon (Si): 1.7%
- Chromium (Cr): 22.8%
- Niobium (Nb): 5.9%
Hardness:
- 1st layer: ~58 HRC
- 2nd layer: 60-64 HRC
Available Diameters:
- Ø 1.6 mm, Ø 2.4 mm, Ø 2.8 mm
Advantages
High abrasion resistance, even at elevated temperatures (up to 450°C).
Suitable for parts exposed to low to moderate impacts.
Smooth fusion, with an even bead appearance and optimal spread.
Slag-free deposit, machinable by grinding or polishing.
Applications
Design of High-Performance Composite Parts, such as:
- Overlay Plates
- Grinding and Mineral Conveying Components
- Dredging Pumps
- Mixers
- Screen Plates
- Chutes, Troughs, and Conveyor Screws
- Knives, Blades, Hoppers, and Tanks
FCW67-650®
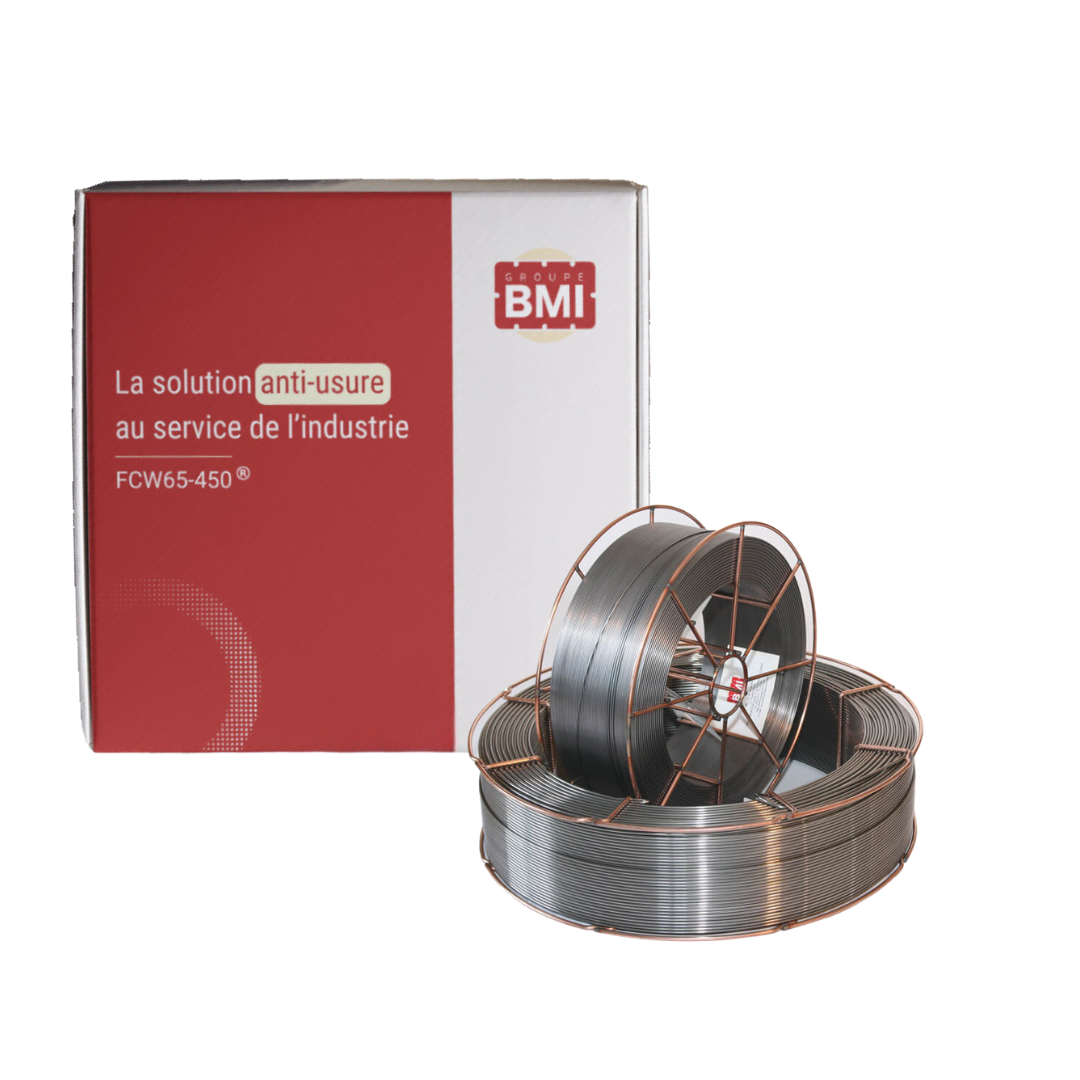
Characteristics
Welding Type: Hardfacing cored wire for open-arc welding (self-shielded, slag-free).
Composition:
- Carbon (C): 6.0%
- Manganese (Mn): 0.4%
- Silicon (Si): 1.0%
- Chromium (Cr): 21.0%
- Molybdenum (Mo): 6.0%
- Niobium (Nb): 6.7%
- Tungsten (W): 1.7%
- Vanadium (V): 0.7%
Hardness:
- 1st layer: ~58 HRC
- 2nd layer: 60-63 HRC
Available Diameters:
- Ø 1.6 mm, Ø 2.4 mm, Ø 2.8 mm
Advantages
Exceptional resistance to abrasion and moderate impacts up to 650°C.
Smooth fusion, optimal spread, and very even bead appearance.
Slag-free deposit, machinable by grinding or polishing.
Ideal for demanding environments, such as steel industries and high-temperature applications.
Applications
- Overlay Plates
- Grinding and Mineral Conveying Components
- Dredging Pumps
- Mixers
- Screen Plates
- Chutes, Troughs, and Conveyor Screws
- Knives, Blades, Hoppers, and Tanks
- Blast Furnace and Sintering Liners
- Extraction Fans, Incinerators, Furnaces, and Mineral Heat Treatment Equipment
FCW70NANO®
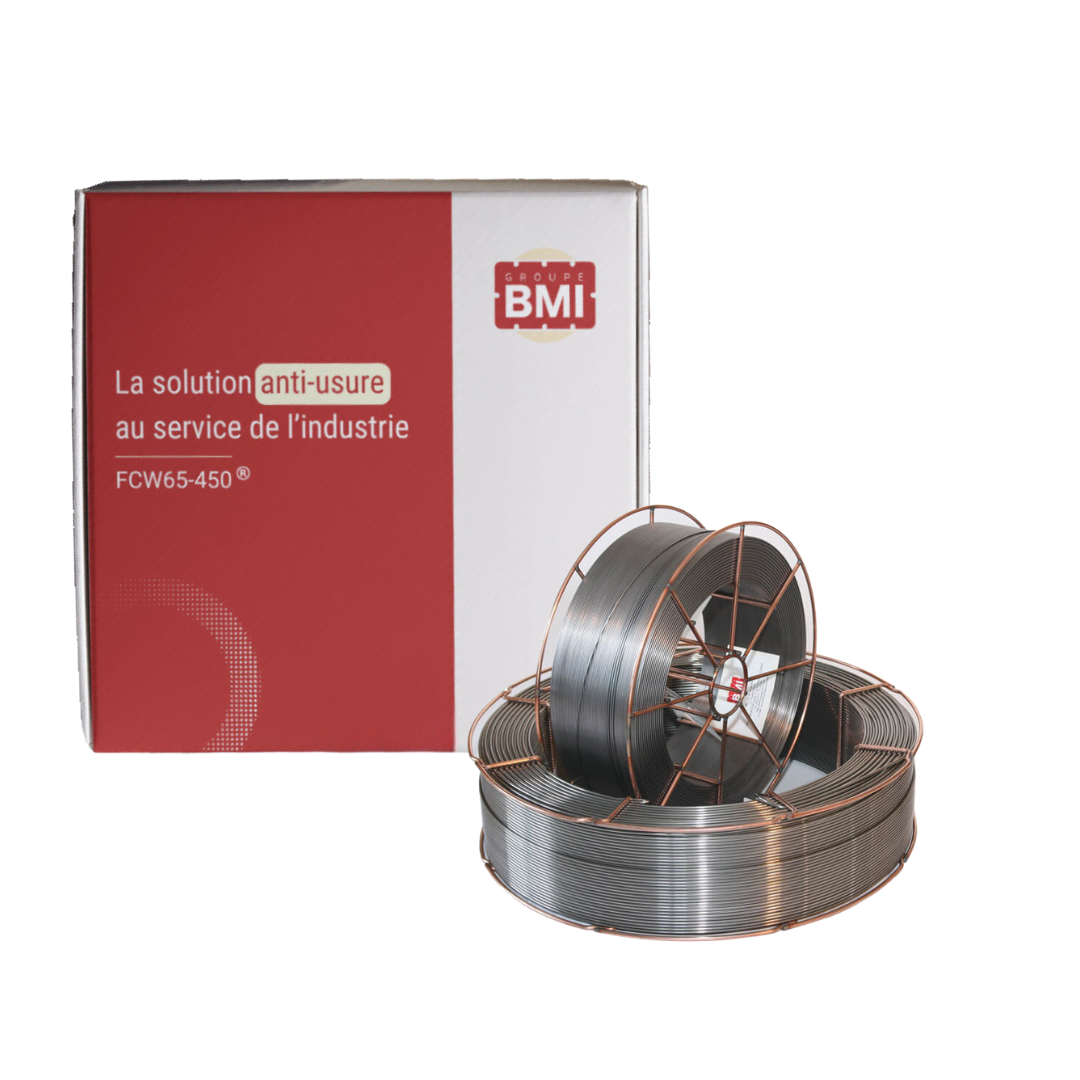
Characteristics
Product Type: Hardfacing cored wire for gas-shielded or self-shielded arc welding.
Composition:
- Chromium (Cr): 21.5%
- Tungsten (W): 6.7%
- Boron (B): 3.6%
- Niobium (Nb): 4.1%
- Molybdenum (Mo): 0.6%
- Carbon (C): 1.1%
- Silicon (Si): 0.7%
- Manganese (Mn): 0.6%
- Iron (Fe): Balance
Hardness: ~66-70 HRC
Structure: Complex carbides and borides dispersed in an austenitic matrix.
Available Diameters:
- Ø 1.2 mm, Ø 1.6 mm, Ø 2.4 mm, Ø 2.8 mm
Advantages
Extreme resistance to abrasion, particularly against high-stress grinding wear and erosion, with no impact resistance required.
High performance from the first layer, reaching 66-70 HRC hardness.
Suitable for single-layer or multi-layer deposits, allowing for thick coatings.
Compatible with existing overlays made with the same product.
Heat resistance up to 750°C, making it ideal for demanding environments.
Applications
- Excavator Buckets
- Grinders
- Extrusion Screws
- Shredders
- Hammers
- Fan Blades
- Sintering Furnaces
FCW60WC®
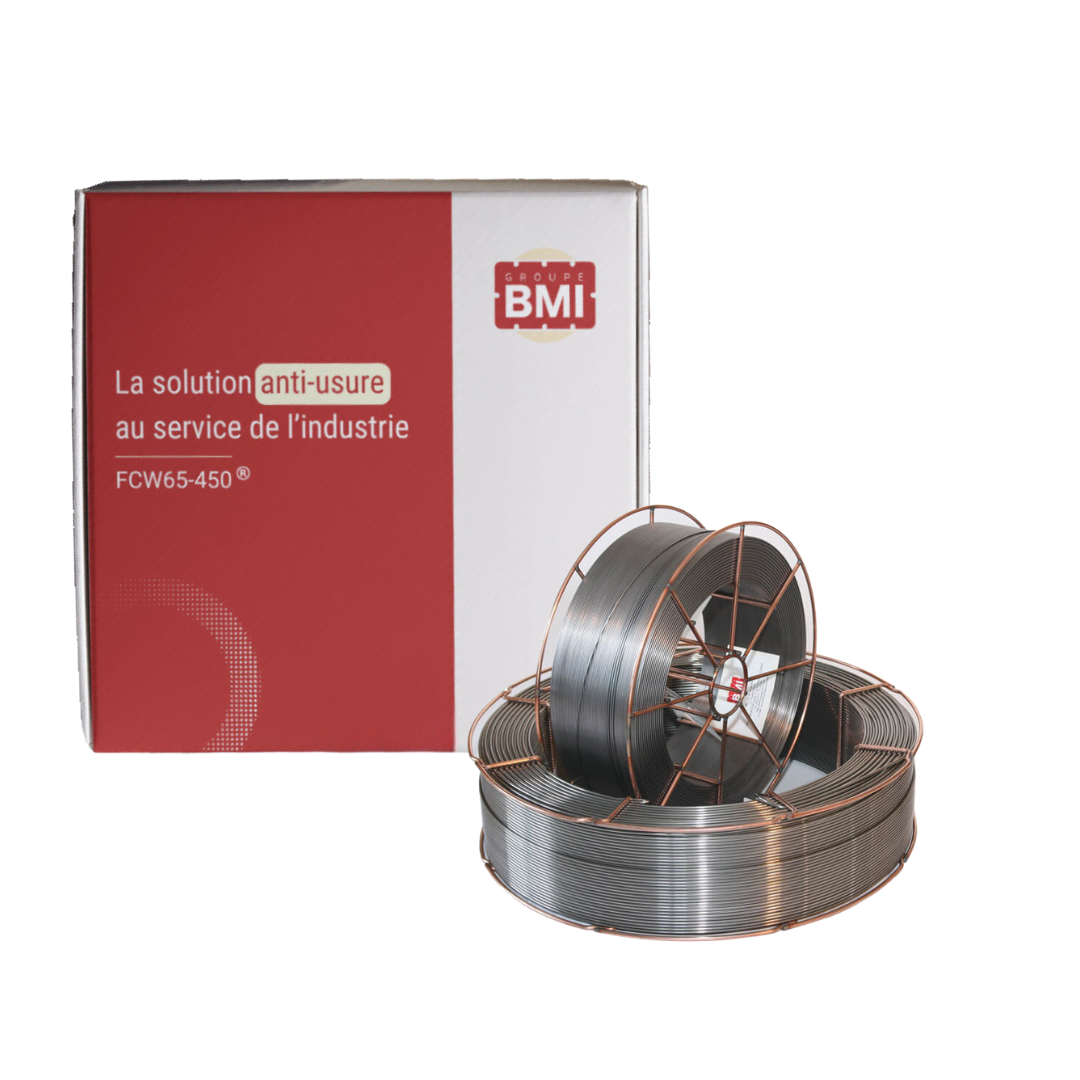
Characteristics
Welding Type: Flux-cored wire for hardfacing under gas protection (Ar+CO₂).
Composition:
- Matrix: Ni-Cr-B-Si (~500-600 HV)
- Tungsten Carbides: (~2300 HV, 50-60% depending on diameter)
Hardness:
- Matrix: ~500-600 HV
- Tungsten Carbides: ~2300 HV
Available Diameters:
- Ø 1.6 mm, Ø 2.4 mm, Ø 2.8 mm
Advantages
- Excellent abrasion resistance due to a high tungsten carbide content.
- Very good corrosion resistance.
- High-toughness deposit, allowing for two-layer application.
- Low heat input welding to preserve carbide properties.
Applications
- Drilling Augers
- Grinders
- Parts for the Clay Industry
- Earthmoving Equipment
- Rubber Mixers
- All components exposed to severe abrasion in mining, steelmaking, and public works
FCW600TIC®
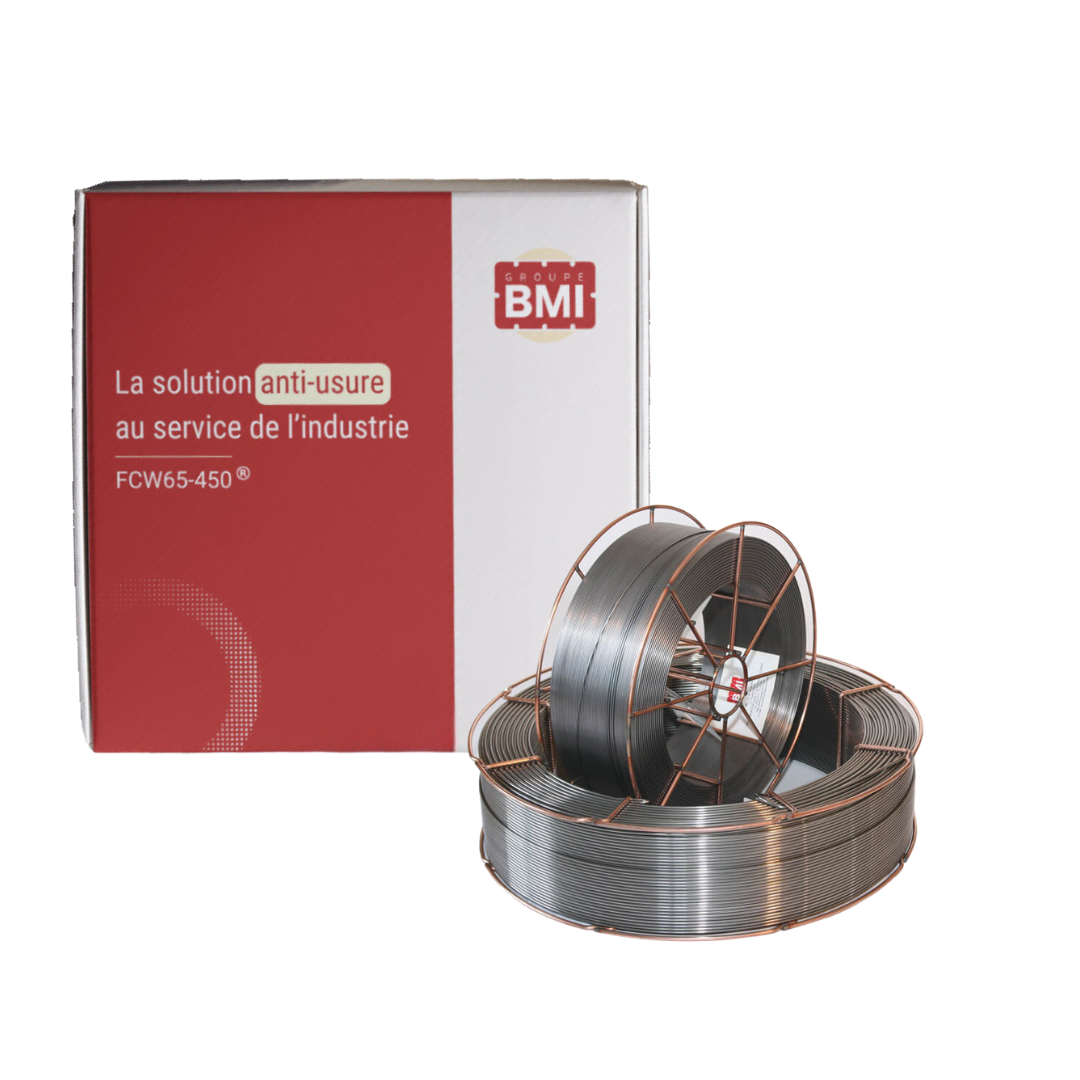
Characteristics
Welding Type: Hardfacing cored wire designed for open-arc welding (self-shielded, no gas protection).
Composition:
- Carbon (C): 1.8%
- Manganese (Mn): 1.2%
- Silicon (Si): 0.8%
- Chromium (Cr): 6.5%
- Molybdenum (Mo): 0.8%
- Titanium (Ti): 5.0%
- Vanadium (V): 0.2%
Hardness:
- 1st layer: ~55-56 HRC
- 2nd layer: ~57 HRC
Available Diameters:
- Ø 1.2 mm, Ø 1.6 mm, Ø 2.4 mm, Ø 2.8 mm
Advantages
Excellent resistance to abrasion, erosion, and combined impacts thanks to a martensitic matrix and a high titanium carbide content.
Smooth fusion, optimal spread, and clean bead appearance.
No slag formation, with a deposit that can be machined by grinding or polishing.
Suitable for demanding environments with high mineral abrasion and moderate impacts.
Applications
- Grinding Hammers and Cylinders
- Excavators
- Disintegrators
- Clod Breakers
- Gravel Processing
- Products for Road Construction
FCW600HB®
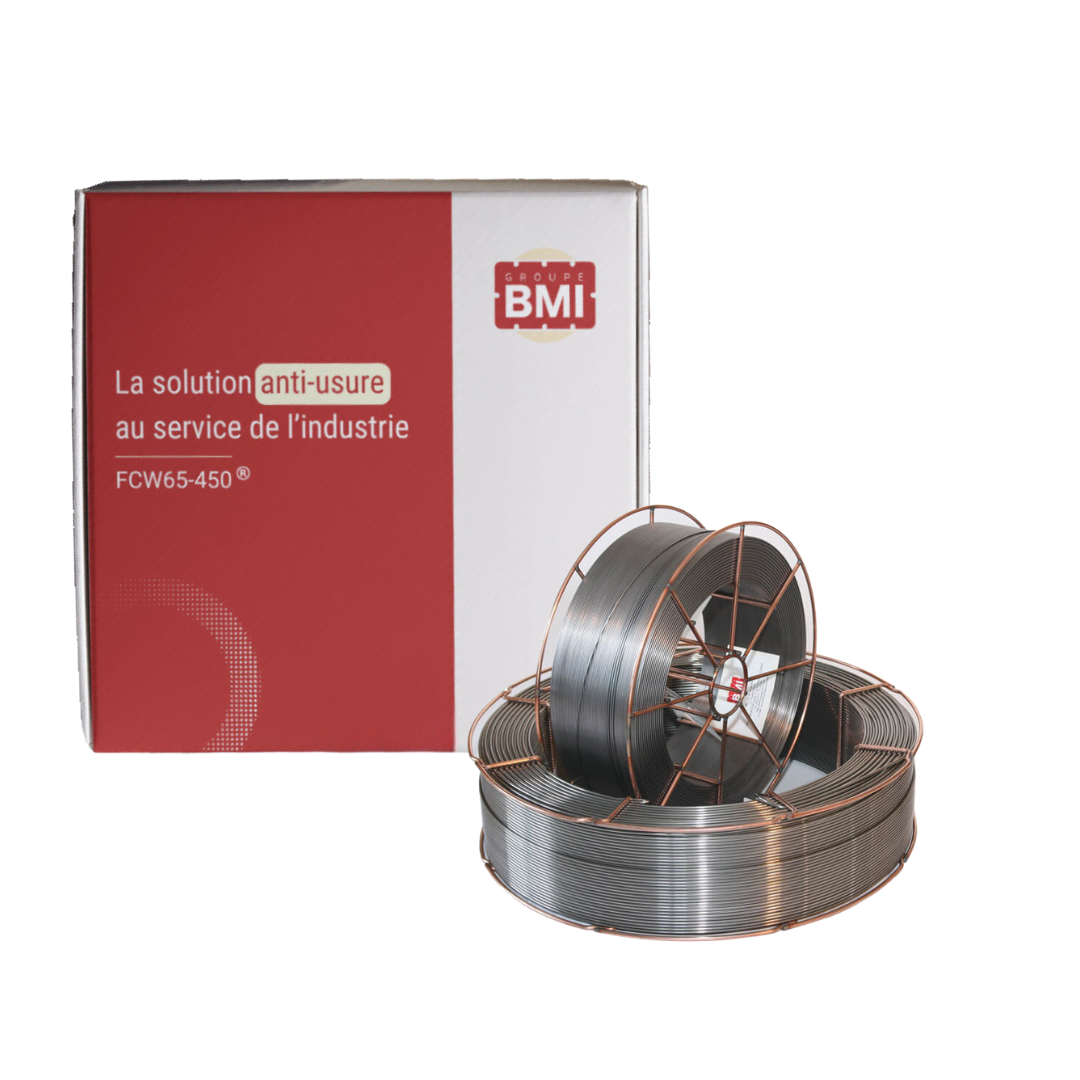
Characteristics
Welding Type: Gas-shielded sealed copper-coated tubular cored wire for hardfacing.
Composition:
- Carbon (C): 0.5%
- Manganese (Mn): 1.2%
- Silicon (Si): 0.7%
- Chromium (Cr): 6.0%
- Molybdenum (Mo): 0.7%
Hardness:
- 1st layer: ~550 HB
- Multiple layers: ~600 HB
Available Diameters:
- Ø 1.2 mm, Ø 1.6 mm
Advantages
High versatility for wear-resistant applications thanks to a fine-grained structure.
20% higher deposition rate on average compared to solid wires.
Unmatched weldability, no moisture absorption, and optimal wire feeding quality.
Machinable by grinding or polishing.
Suitable for parts exposed to metal-to-metal wear and low-stress abrasion, with or without significant impacts.
Applications
Manufacturing of high-performance composite parts, such as:
- Shear Shredders
- Blade Shredders
- Grinding and Conveying Components in the Mineral Industry
- Mixers
- Dredging Pumps
FCW650HB®
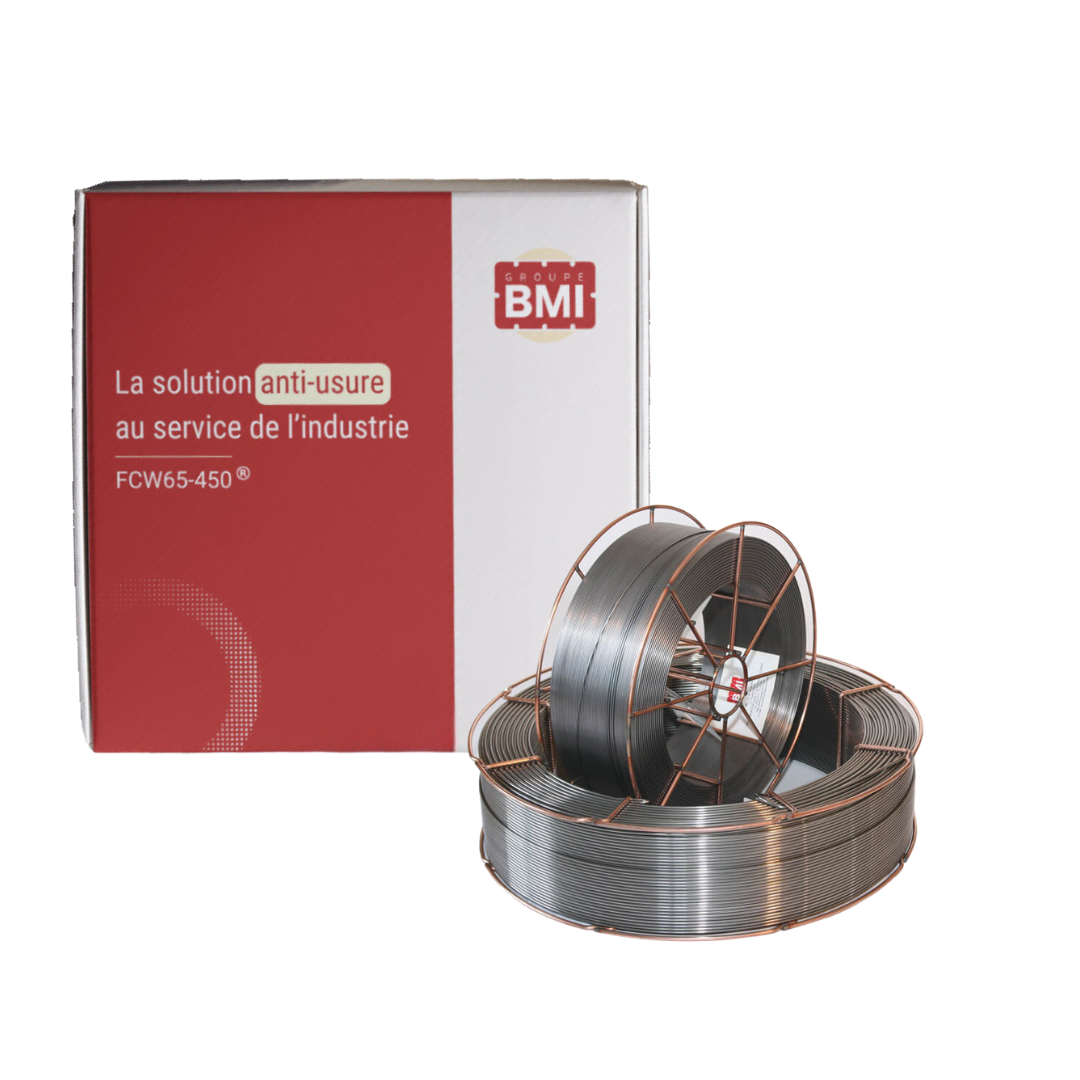
Characteristics
Welding Type: High-fill copper-coated tubular cored wire for semi-automatic hardfacing under gas protection.
Composition:
- Carbon (C): 0.5%
- Manganese (Mn): 1.3%
- Silicon (Si): 1.3%
- Chromium (Cr): 5.6%
- Molybdenum (Mo): 1.3%
Hardness:
- Single layer: ~57 HRC
- 2-3 layers: ~62 HRC
Available Diameters:
- Ø 1.2 mm, Ø 1.6 mm
Advantages
Excellent resistance to abrasion, metal-to-metal wear, and heavy impacts.
Maintains performance up to 500°C.
20% higher deposition rate compared to solid wires.
Suitable for flat, edge, and vertical-up hardfacing applications.
Applications
- Bucket Teeth and Blades
- Grinding Hammers
- Drill Bits
- Cutting Tools
- Shredding Tools
- Conveyor Chains